数控车床利用磨耗实现快速对刀
数控车削对刀是加工前的必要准备,要求对刀准确、快速。数控车刀的精度直接关系到零件的精度,刀具的熟练程度会影响产品的生产效率,尤其是在单件生产中更为突出。因此,提高数控车床的刀具速度,可以提高产品的加工效率。为了提高生产效率,我们采用磨耗对刀的方法实现了数控车床的快速对刀。
一、对刀原理
对刀的目的主要是为了建立工件坐标系和确定刀具长度偏差,即确定编程坐标系原点在机床坐标系中的位置。目前有试切法对刀和采用对刀仪对刀两种方法。试切法对刀是实际中应用最多的一-种对刀方法。
加工如图1所示的零件,至少用到3把刀,即外圆车刀、切槽刀和螺纹车刀,以右端面为编程原点。现以外圆车刀对刀为例进行试切法对刀步骤的说明。基本所有数控车床试切法对刀都在工件和刀具装夹完毕后,驱动主轴旋转完成下面两个步骤;
(1)移动刀具试切工件右端面,保持刀具在z方向位置不变,沿X方向退刀,并在FANUC系统中的[工具补正/形状]界面下,在Z坐标下输入“Z0",按下[测量],则Z方向的刀偏就输入到系统中。
(2)移动刀具至工件试切一-段外圆,然后保持X坐标不变,向Z轴移动使刀具离开工件,测量试切后的工件外圆直径为d,并在FANUC系统中的[工具补正/形状]界面下,在X坐标下输人“Xd",按下[测量],则X方向的刀偏就输人到系统中。其他两把刀具的对刀重复以上步骤即能完成。
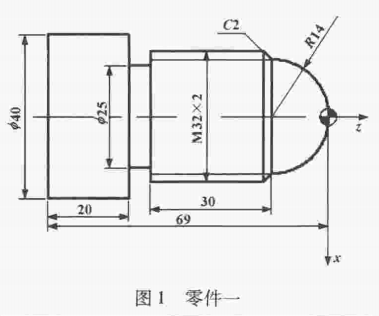
二、利用磨耗实现快速对刀的方法和步骤
在数控车床中,磨擦值一般用于加工第一件,测量发现,人的大小,如果不想改变程序条件,可以微调磨擦值,以保证零件的加工精度;或者更有用的是,加工一段时间后,刀具的损耗,但也可以使用,为了保证加工尺寸,对磨损值进行微调也可以保证零件加工的精度。但是,在单件生产中,由于每个零件都需要调整,效率很低,但如果磨损得到很好的利用,也可以减少刀具的匹配,提高刀具的匹配速度。
由于数控车床在加工零件时,大部分零件的加工刀具基本上变化不大,一般是用圆柱车刀、开槽刀、螺纹车刀、孔车刀都能完成,所以安装刀具后基本不需要更换刀体,如果刀片磨损,更换刀片上的管路。如果第一个工件用这些刀具加工,第二个工件不需要再用三把刀加工,但只有一把刀才能解决问题。如图3所示的零件加工还需要3把刀具(圆柱车刀、开槽刀和螺纹车刀)。如果采用一般的方法,3把刀在加工前都要调整,但这种效率比较慢。如果采用减少磨损的方法,则只需再次调整其中一个刀具,而不再需要调整其他刀具。
下面就是利用磨耗减化对刀的步骤和方法:
(1)以其中的一把刀作为基准刀(如外圆车刀),进行Z方向的对刀。移动刀具试切工件右端面,保持刀具在Z方向位置不变,沿X方向退刀,并记录下此时的机床坐标系中的Z坐标值。
(2)将刚记录下的Z坐标值与上次对刀中的Z 偏置中的Z值相减,将两次的差值作为刀具长度磨耗值输人到对应刀号的磨耗中,其他两把刀的差值同样处理。
(3)在X方向上由于都是以零件的轴线建立编程坐标系,故不管怎么变化,X方向的刀偏值始终不变,故磨耗值都为0。
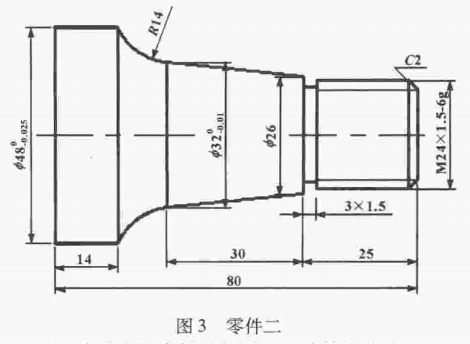
三、结论
总之,利用磨损实现车床的快速对刀可以概括为:Z磨损=Z2-Z1-L长度
这里,Z2是第二次对刀时Z方向的机床坐标值,Z是第一次对刀时的刀具偏差值,L长度是对刀时刀点与编程坐标系原点的Z方向距离,然后在图4中的[刀具修正/磨损]界面下、Z坐标磨损量应输入Z坐标磨损量。同样,其他刀具的z坐标磨损也相应地输入到z磨损中。从以上可以看出:在单件或小批量生产中,使用磨具可以快速实现对刀,提高生产效率。
|