对刀仪对刀原理解析
一、刀位点
刀位点是刀具上的一个基准点,刀位点相对运动的轨迹即加工路线,也称编程轨迹。
二、对刀和对刀点
对刀是指操作者在启动数控程序前,通过一定的测量手段使刀尖与对刀仪重合。该对刀仪可用于对刀。其操作相对简单,测量数据相对准确。在数控机床上定位夹具并安装零件后,使用量块、塞尺、千分表等,用数控机床上的坐标对刀具进行设置。对于操作者来说,刀具点的确定是非常重要的,它直接影响到零件的加工精度和程序控制的精度。在批量生产过程中,应注意刀位的重复精度。操作人员需要加深对数控设备的了解,掌握更多的刀具设置技能
1、对刀点的选择原则
在机床上容易找正,在加工中便于检查,编程时便于计算,而且对刀误差小。
对刀点可以选择零件上的某个点(如零件的定位孔中心),也可以选择零件外的某一点(如夹具或机床上的某一点),但必须与零件的定位基准有一定的坐标关系。
提高对刀的准确性和精度,即便零件要求精度不高或者程序要求不严格,所选对刀部位的加工精度也应高于其他位置的加工精度。
选择接触面大、容易监测、加工过程稳定的部位作为对刀点。
对刀点尽可能与设计基准或工艺基准统一,避免由于尺寸换算导致对刀精度甚至加工精度降低,增加数控程序或零件数控加工的难度。
为了提高零件的加工精度,对刀点应尽量选在零件的设计基准或工艺基准上。例如以孔定位的零件,以孔的中心作为对刀点较为适宜。
对刀点的精度既取决于数控设备的精度,也取决于零件加工的要求,人工检查对刀精度以提高零件数控加工的质量。尤其在批生产中要考虑到对刀点的重复精度,该精度可用对刀点相对机床原点的坐标值来进行校核。
2、对刀点的选择方法
对于数控车床或车铣加工中心类数控设备,由于中心位置(X0,Y0,A0)已有数控设备确定,确定轴向位置即可确定整个加工坐标系。因此,只需要确定轴向(Z0或相对位置)的某个端面作为对刀点即可。
对于三坐标数控铣床或三坐标加工中心,相对数控车床或车铣加工中心复杂很多,根据数控程序的要求,不仅需要确定坐标系的原点位置(X0,Y0,Z0),而且要同加工坐标系G54、G55、G56、G57等的确定有关,有时也取决于操作者的习惯。对刀点可以设在被加工零件上,也可以设在夹具上,但是必须与零件的定位基准有一定的坐标关系,Z方向可以简单的通过确定一个容易检测的平面确定,而X、Y方向确定需要根据具体零件选择与定位基准有关的平面、圆。
对于四轴或五轴数控设备,增加了第4、第5个旋转轴,同三坐标数控设备选择对刀点类似,由于设备更加复杂,同时数控系统智能化,提供了更多的对刀方法,需要根据具体数控设备和具体加工零件确定。
对刀点相对机床坐标系的坐标关系可以简单地设定为互相关联,如对刀点的坐标为(X0,Y0,Z0),同加工坐标系的关系可以定义为(X0+Xr,Y0+Yr,Z0+Zr),加工坐标系G54、G55、G56、G57等,只要通过控制面板或其他方式输入即可。这种方法非常灵活,技巧性很强,为后续数控加工带来很大方便。
一旦因为编程参数输入错误,机床发生碰撞,对机床精度的影响是致命的。所以对于高精度数控车床来说,碰撞事故要杜绝。
3、碰撞发生的最主要的原因:
a.对刀具的直径和长度输入错误;
b.对工件的尺寸和其他相关的几何尺寸输入错误以及工件的初始位置定位错误;
c.机床的工件坐标系设置错误,或者机床零点在加工过程中被重置,而产生变化,机床碰撞大多发生在机床快速移动过程中,这时候发生的碰撞的危害也最大,应绝对避免。
所以操作者要特别注意机床在执行程序的初始阶段和机床在更换刀具的时候,此时一旦程序编辑错误,刀具的直径和长度输入错误,那么就很容易发生碰撞。
在程序结束阶段,数控轴的退刀动作顺序错误,那么也可能发生碰撞。
为了避免上述碰撞,操作者在操作机床时,要充分发挥五官的功能,观察机床有无异常动作,有无火花,有无噪音和异常的响动,有无震动,有无焦味。发现异常情况应立即停止程序,待机床问题解决后,机床才能继续工作。
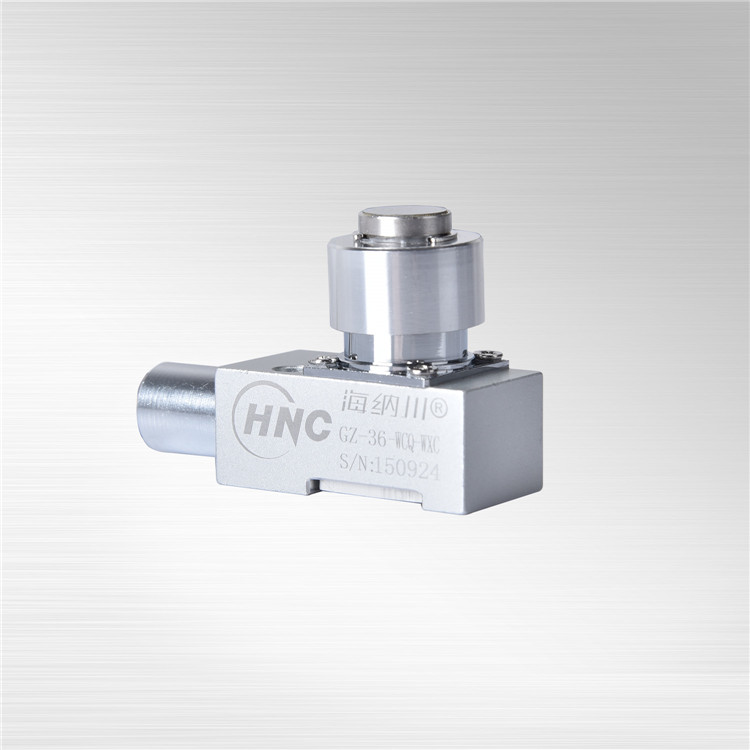
三、零点漂移现象
零漂现象是由于数控设备周围环境的影响,在相同的切削条件下,对于相同的设备,使用相同的夹具、数控程序、刀具,加工相同的零件,出现加工尺寸不一致或精度降低的现象。
零漂现象主要表现在数控加工精度的降低或可以理解为数控加工精度的不一致。零漂现象是数控加工过程中不可避免的现象,由于数控设备具有普遍性,一般受数控设备周围环境的影响,严重时会影响数控设备的正常工作。影响零点漂移的原因有很多,包括温度、冷却液、刀具磨损、主轴转速和进给速度。
四、刀具半径补偿
在零件轮廓工中,由于刀具总有一定的半径如铣刀半径,刀具中心的运动轨迹并不等于所需加工零件的实际轨迹,而是需要偏置一个刀具半径值,这种偏移习惯上成为刀具半径补偿。因此,进行零件轮廓数控加工时必须考虑刀具的半径值。需要指出的是,UG/CAM数控程序是以理想的加工状态和准确的刀具半径进行编程的,刀具运动轨迹为刀心运动轨迹,没有考虑数控设备的状态和刀具的磨损程度对零件数控加工的影响。因此,无论对于轮廓编程,还是刀心编程,UG/CAM数控程序的实现必须考虑刀具半径磨损带来的影响,合理使用刀具半径补偿。
五、刀具长度补偿
在数控铣、镗床上,当刀具磨损或更换刀具时,使刀具刀尖位置不在原始加工的编程位置时,必须通过延长或缩短刀具长度方向一个偏置值的方法来补偿其尺寸的变化,以保证加工深度或加工表面位置仍然达到原设计要求尺寸。
六、刀具补偿
经过一定时间的数控加工后,刀具的磨损是不可避免的,其主要表现在刀具长度和刀具半径的变化上,因此,刀具磨损补偿也主要是指刀具长度补偿和刀具半径补偿。
七、装夹原点
装夹原点常见于带回转(或摆动)工作台的数控机床和加工中心,比如回转中心,与机床参考点的偏移量可通过测量存入数控系统的原点偏置寄存器中,供数控系统原点偏移计算用。
八、机床坐标系
数控机床的坐标轴命名为机床直线运动的笛卡尔坐标系,其坐标命名为X、y、Z,一般称为基本坐标系。以X、y、Z坐标轴或与X、y、Z坐标轴平行的坐标轴为中心的运动分别称为a轴、b轴、c轴。a B C的正方向是根据右手螺旋定律确定的。
Z轴:一般将传递切削力的主轴定义为Z轴。对于具有刀具旋转的机床,如镗床、铣床、钻床等,刀具旋转的轴称为Z轴。
X轴:X轴通常平行于工件夹紧面,垂直于Z轴。对于带有刀具旋转的机床,如卧式铣床和卧式镗床,从机床主轴到工件的方向上,右手方向是X轴的正方向。当Z轴垂直时,对于单柱立式铣床等机床,从刀轴方向到立柱方向,右手方向是X轴的正方向。
y轴:y轴垂直于x轴和z轴,其方向可根据已确定的x轴和z轴根据直角坐标系确定。
旋转轴的定义也符合右手定则。绕x轴的旋转是a轴,绕y轴的旋转是b轴,绕z轴的旋转是c轴。
机床的原点就是机床坐标系的原点。机床上有一些固定的基准线,如主轴中心线;还有一些固定的基准面,如工作台、主轴端面、工作台侧面等。当机床坐标轴的回到原来的手动点,机床的原始点的位置可以由参考线和参考平面之间的距离在每个坐标轴组件,这是数控机床的操作手册中描述。
|