数控车床对刀方法研究
近年来,计算机技术、信息技术和自动化不断发展。现代制造业的发展已经有了很大的进步,并转变为基于数字化的现代制造技术。高速、高精度、智能化是数控机床发展的最终方向。
1.数控车床的对刀原理
数控车床上的刀具理论对刀具的展开起着指导作用,使操作者能够保持良好的工作原理和良好的刀具设计。刀具的最终目的是确定工件在机床工作面上的位置;此时,操作者必须建立编程坐标系,使机床坐标系与编程坐标系相对应,最终目的是确定刀具点相对于机床坐标系的位置值。
1.1机床、工件坐标系
数控机床的坐标系一般定义为坐标为原始坐标的坐标系。每台车床的机床坐标系在出厂前由专业人员建立,用户不得更改。数控机床的手动调零必须在意外断电或故障后进行。此操作的目的是使刀架或工作面达到机床的零点。只有回到机床原点,机床坐标系才能正确地加工零件。
数控车床的操作和功能更简单,在大多数情况下,刀具是通过切割来调整的。组合轴的零件,如图2所示,毛坯直径为26毫米,实际转化为四个,分别为:90°手推车的圆刀和直刀,从一个口罩切割到狭缝(刀,悬弧以上的车,螺纹匕首,直端螺纹,最后切割刀具。
工件坐标系(编程坐标系)定义为以工件为原点建立的坐标系[3]。这个坐标系是由工作人员(操作员)人工固定的。理想情况下,原点可以是任意点。但是如果工件坐标系的原点选择不正确,会给以后的编程带来很大的问题。选择零件坐标原点时,必须考虑原点与零件尺寸、固定点之间的关系。数控车床一般选择工件右侧面中心的工件零点,保证机床的坐标系与工件坐标系相结合。
1.2刀的位置和位置
手动移动刀具和刀尖,直到其与定位块上部对齐,同时将坐标显示值设置为零,然后带回起始位置读取坐标值。这种方法应保证刀尖与定位块对准,对准精度直接影响到刀的精度。
工件坐标系、机床坐标系、切削点和切削位置之间的关系如图1所示。
切削点决定机床上刀具的固定点和参考点,为了精确地找到切削点相对于工件坐标系的加工位置,必须首先确定切削点。数控系统是基于间接控制每个刀具的运动轨迹来控制刀具的位置。在数控车床系统中,术语“刀具”是指刀具的尖端。然而,切削位置的选择因刀具而异。因此,刀具的目的是将刀具的切削点保持在编程坐标系中刀具的起始点,这有助于通过数控系统对工件进行后续控制,使被车削的零件与固定点具有精确的尺寸关系,并确保加工零件所需的精度。由于被加工零件使用多个刀具进行编程加工,因此在换刀后,还必须确保新刀具的切削点与标准刀具的切削点相结合。由于刀具位置之间存在误差,操作者可以通过刀具补偿功能消除误差。
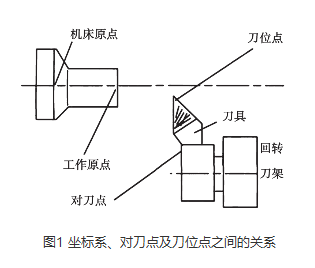
2数控加工中的基本刀具方法
由于采用不同的位置检测模式,手动刀调整分为相对和绝对方程。刀方程可采用三种方法。
一般来说,最常见的打刀方式有手动打刀、外刀打刀、空管打刀和自动打刀。
(1) 用钢尺直接测量,方法简单,但精度不高。
(2) 选择切割点时,操作者必须遵循以下原则:(1)便于数学计算和简化编程;(2)便于寻找对中刀具;(3)便于加工控制;(4)加工误差小;5)避免与机床和工件碰撞;(6) 便于零件的拆卸。
(3) 切割粗糙面,使用卡尺测量其尺寸,并间接计算表面尺寸。这种方法包括修正刀,这是最准确的。在实践中,数控车床一般使用三种以上的刀具进行车削,使参考刀具和非参考刀具包含在所有刀具中。在刀的绝对手动调整中,首先要选择精度较高的基准刀,然后使用灵活的步进功能,直接或间接测量北侧刀尖与基准刀尖之间的实际距离。这个距离是刀具的切削量。总之,手动方法允许刀具通过转动工件,使用“测试切割-测量-调整(补偿)”模式进行对齐。这种模态分析方法简单、成本低廉,但效率较低,更适合于经济型数控车床。点攻击机要求操作者在切割前预先设定并测量实际参数,然后将测量结果记录在相应的寄存器中,该寄存器安装在数控车床上。该方法适用于钻铣床类数控机床,具有加工效率高、精度高等优点,但成本高、结构复杂。
ATC刀具必须在机床上配备显微镜,显微镜中的十字交叉点必须位于机床坐标系中的恒定点上。当测量数据时,手动脉冲发生器移动刀具,使虚拟刀具的刀尖与反射镜的交点重合。这时,数控车床自动计算出从切削点到原点的距离,同时保持相应的切削面积。这种方法确实包含了每次在升降镜上进行装载和卸载以及手动操作时必须出现的错误。这种方法的优点在于能自动精确地测量刀具参数,并能自动修正刀具的补偿值,同时保证了较高的工作效率,可以与高水平的机床进行比较。
3数控车床精调实例
数控机床的加工零件用CN代码编程,完成刀架的运动和零件的运动。编程加工时,必须以工件坐标系为基准。刀架的运动是在机床坐标系上进行的,因此工件坐标系与机床坐标系无关,二者相互独立。由于数控系统不知道工件和刀具在机床中的协调位置,因此在这个阶段,机床不能根据操作员编写的程序进行加工。加工前,必须加工刀具,告知机床零件和刀具的精确位置。为了确定切削点和机床坐标零点之间的联系,在工件坐标系中找到切削点的起始位置就足够了,该点是相对于切削点的点。
(1) 为了精确调整刀具,按照以下步骤进行试切。刀具偏差的调整。使用输入面板上的“刀具偏置”功能,操作员进入刀具补偿寄存器,其中每个刀具补偿号对应一个一维偏置:X轴和Z轴的偏置值、刀具端圆弧半径的R值和刀具端位置的T值,如表1所示。使用X轴和Z轴刀具,通过移除刀具,选择4号刀具并将其与B点对齐,同时将面板上的X和Z坐标值作为刀具相对于4号刀具X和Z轴的偏差考虑在内;其余两个刀具的偏移量以相同方式调整。
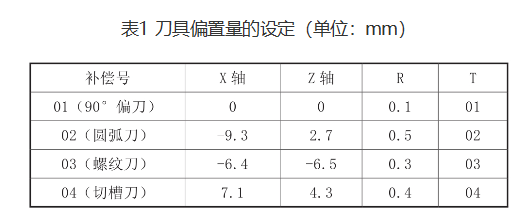
(2) 定位工件坐标系的原点。选择面板上的刀1,并在点模式或步进模式下将刀1移动到工件的外圆,以确保x方向值不会改变。用游标尺对刚性托架X1圆的外径值进行酸洗和测量;再次将刀具1移到工件的尺寸端,确保Z方向值不变,灯的右端保持在-X1。
(3) 确定攻击点。在图2中,对刀具的攻击点被定义为工件毛坯外部的点a(70,30),同样,在点模式或逐步模式下,对刀具的刀具之一被放置在位置X=70和Z=30。在程序中,第一个指令使用G92(G50)X70 Z30在车床上工作。
结论
在实际中,工件的结构是可变的,但刀具的工作过程是一致的。因此,在实际操作过程中,要对刀具进行精确的调整,就必须进行多次操作,积累经验,提高操作能力。总之,对刀仪的精度直接关系到被加工零件的质量,同时在生产加工中起着重要的作用。实践训练对于培养数控技术人员,提高学生的综合素质和实践技能是非常有益的。
|